Designing Stone Anchors
Excavations throughout Europe have found stone used for shelter as far back as 12,000 B.C. The Egyptians built the pyramids around 2550 BC and the Romans established a stone quarry around 173 BC. Today, stone remains one of the strongest and most durable building products on the planet. When using stone as a veneer, engineering and design are critical factors in a successful building project. The majority of stone projects are unique and require custom anchors.
For slab-type anchored veneer, the International Building Code specifies a minimum of four anchors per unit with tie spacing not exceeding 24 inches. The maximum area of a unit is limited to 20 square ft. Veneer ties for slab-type veneer are required to resist two times the weight of the anchored veneer in tension or compression. Wire stone anchors must be a minimum of 9 gauge diameter (.1483 inches). Non-wire stone anchors are to have a minimum width of 1”.
The TMS402 Building Code Requirements and Specification for Masonry Structures list several references and guidelines for adhered veneer. Anchored dimensional stone is not currently covered under the code and is considered a “special system” that requires engineering.
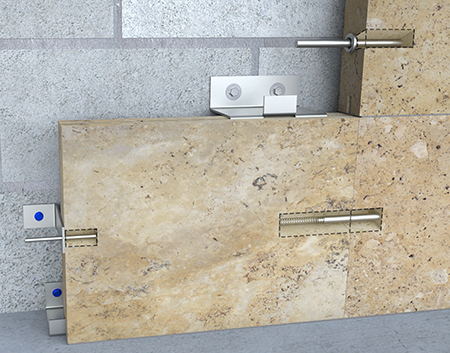
Anchored stone veneer
Stone veneer units are limited to a maximum thickness of 10 inches. Anchored stone veneers must be designed by a licensed engineer through a three-step process:
- Analyze the stone: Find the stress point of the stone. Use a safety factor of 5-1. Start with two anchors on top and two on the bottom at quarter points. The goal is to support the stone without cracking. Add more anchoring points if necessary.
- Evaluate the backup wall. Typical backup walls are concrete, CMU, wood or metal studs. If the stone veneer is going over an older existing concrete or CMU backup wall, pullout tests should be done to verify the wall is capable of holding the veneer.
- Design the stone anchors and fasteners to transfer the loads from the veneer to the backup. The distance from the backup wall to the center of the stone is fixed. Loads can be increased by making the anchor thicker and/or wider and adding more anchors. Use a safety factor of 4-1 for the anchors. Finally, analyze the fasteners for the attachment of the anchor to the backup.
The vast majority of stone anchors are manufactured from Type 304 stainless steel or Type 316 for marine environments. Mechanical anchorage is achieved by cutting a kerf in the stone for placement of anchor bends or by drilling holes for placement of pins. Heckmann Building Products discourages the use of Plain Steel Hotdip Galvanized After Fabrication anchors for use in exterior stone projects.
Manufacturing minimums
Bends: U-Shaped Anchors with bends on each end require an od length (B) that is greater than the smallest bend. The chart below shows minimum bends for typical stone anchors less than 8” wide.
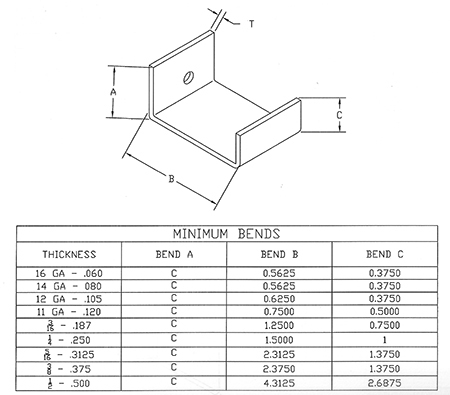
Holes: The tension pullout strength decreases when the hole is further from the bend. The greater the distance the more prying action on the bend.
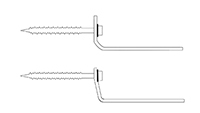
In the fabrication process the holes are burned or punched before the anchor is bent. If the hole is too close to the bend it will distort when the bend is made. For anchors under 8” wide, this is the formula for the minimum distance from the inside dimension of the bend to the start of the hole:
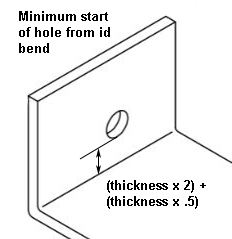
(thickness x 2) + (Thickness x .5)
If your anchor is 1/8” thick, then (.125 x 2) + (.125 x .5) = 0.3125 = 5/16”
If you are designing a short U-Type anchor, make sure the hole is located high enough to get the fastener installed.
Engineering
Bids for anchored stone veneer projects should verify the engineering is factored into the bid. The engineering responsibility varies from job to job. It can be factored into the architecture/engineering work or be the responsibility of the mason contractor, general contractor or the stone provider. A few times a year, we get a call where stone already is on the jobsite, and the contractor is looking for “off the shelf” stone anchors (which do not exist). A mad scramble ensues with the mason contractor, general contractor, engineer and stone provider figuring out who will pay for the engineering since nobody put it into the bid. During this time, the job usually gets put on hold. Designing the anchors and figuring out the dimensions also ensures the bidding process can include the correct sized anchors. The anchor costs are unknown until the engineering determines the actual style, thickness, and dimensions of the anchor.
Anchor Choices
The four most common types of stone anchors are shown below. The pin type usually is installed with the pin loose, so the anchor can be attached to the backup and the hole used as a template to drill down into the stone. The top stone is then brought into place, and a hole is drilled up. The three anchors with bends are used at the top (Z-Type), bottom (U-Type) and between two stones (Split-bend Type). The engineering process will determine the width and thickness of these anchors.
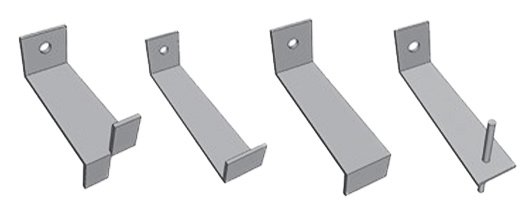
Split-bend Type, U Type, Z Type and Pin Type anchors
For both adhered and anchored veneers under the code:
- Backup wall must be designed to resist water penetration and be covered with a continuous water-resistant membrane unless the sheathing is already water resistant and the joints are sealed.
- Flashing and weep holes in exterior veneer must be designed and detailed to resist water penetration into the building interior.
- Design and detail the veneer to accommodate differential movement.
There are a multitude of anchors for special conditions. Heckmann Building Products can work with your design team to verify your anchor configuration is possible. Here are some of the more popular styles of stone anchors:

Submittal sheets for each of these anchors are on the Heckmann website www.heckmannanchors.com. Input the product number in the search bar at the top of the web page, go to the product page and click on the Submittal Sheet under Resources.
Unique Custom fabrications are quite common for stone anchors. Here are few we have made over the years.
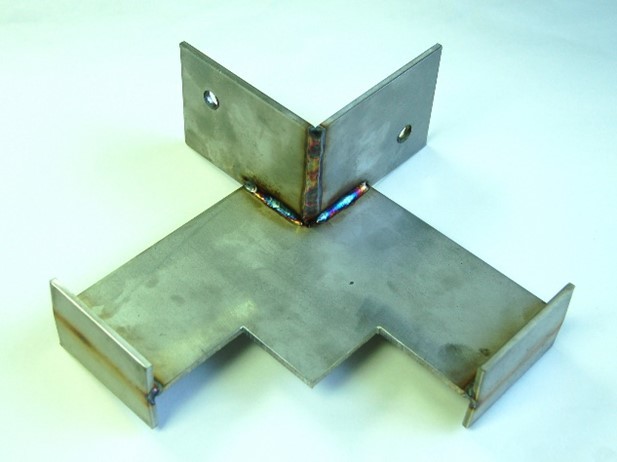
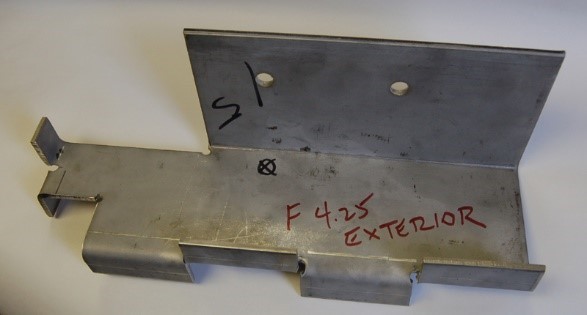
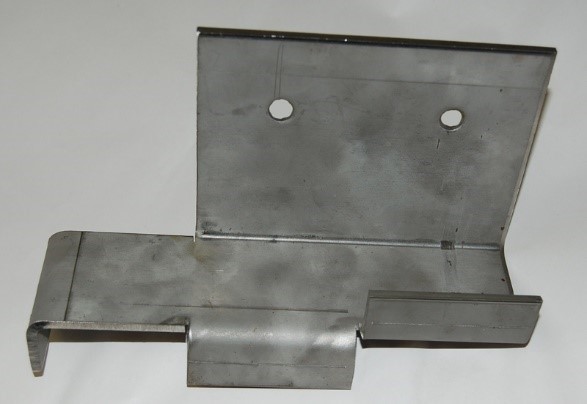
Additional Guidance for stone anchor design
Cast Stone Institute: www.caststone.org. Go to “technical resources” and check out “anchors and Inserts”, “Typical Details” and “Value Engineering”.
Indiana Limestone Institute of America: www.iliai.com. Go to “Technical Information”. Download their “Indiana Limestone Handbook” 22nd edition. This is an excellent publication that shows many case studies of limestone projects along with wall details and case studies.